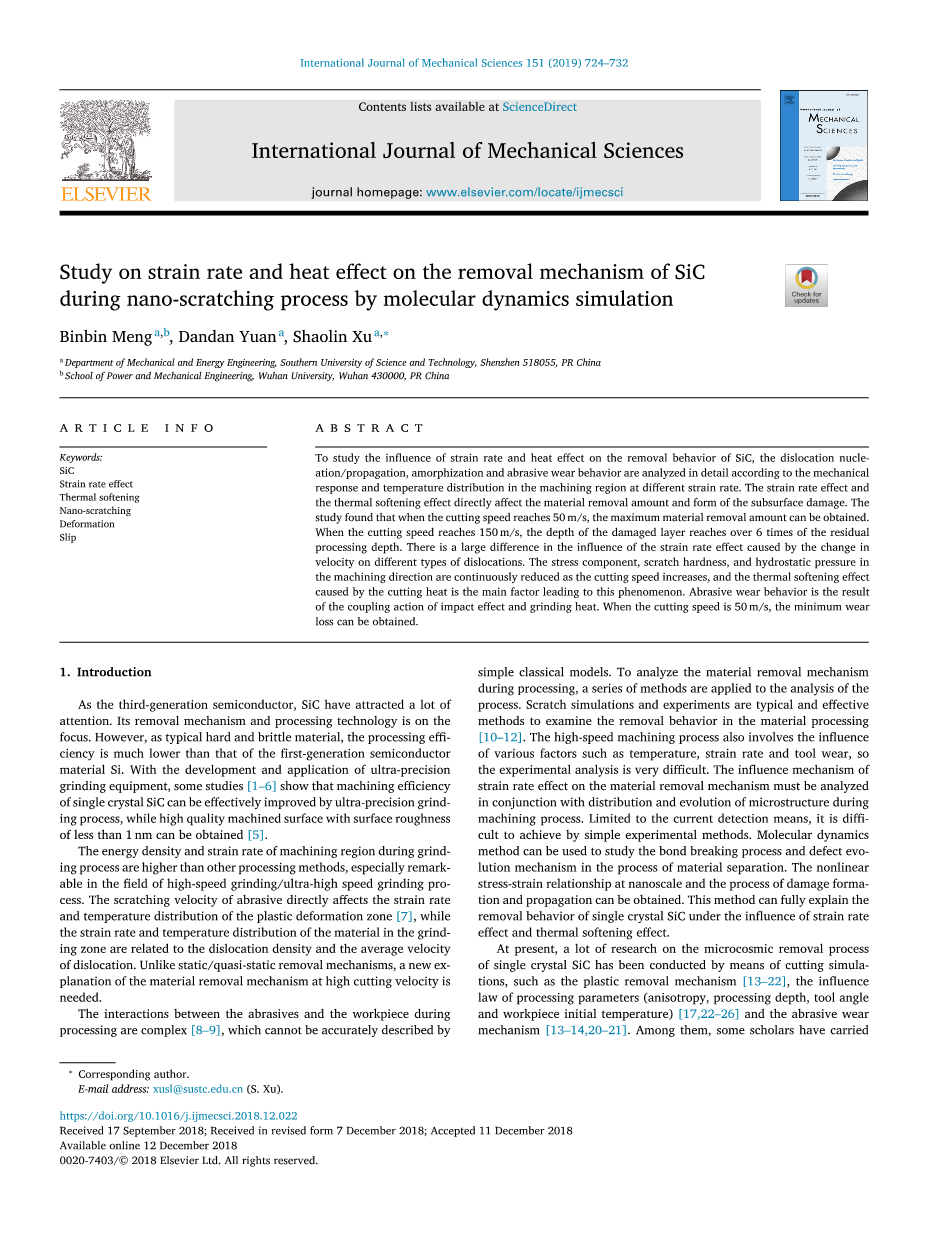
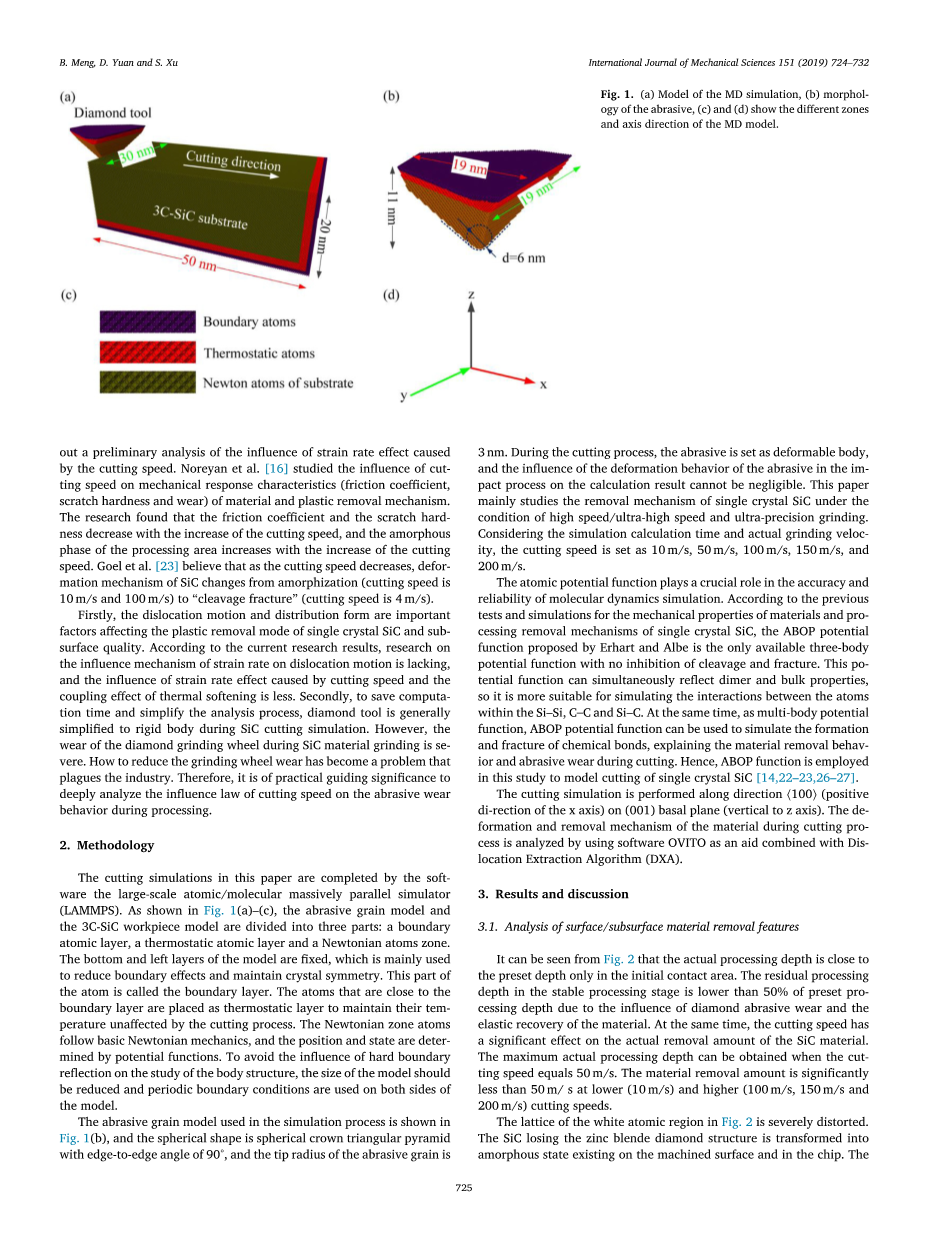
英语原文共 9 页,剩余内容已隐藏,支付完成后下载完整资料
译文 纳米划痕过程中应变率和热效应对碳化硅去除机理的分子动力学模拟研究
文章信息
关键词: 碳化硅 应变率效应 热软化纳米划痕变形 滑移系 摘要 为了研究应变率和热效应对碳化硅去除行为的影响,根据不同应变率下加工区域的力学响应和温度分布,详细分析了位错形核/扩展、非晶化和磨粒磨损行为。应变率效应和热软化效应直接影响材料去除量和亚表面损伤的形式。研究发现,当切削速度达到50 m/s时,可以获得最大的材料去除量。当切削速度达到150 m/s时,损伤层深度达到剩余加工深度的6倍以上。由速度变化引起的应变率效应对不同类型位错的影响有很大差异。随着切削速度的增加,加工方向上的应力分量、划痕硬度和流体静压力不断减小,由切削热引起的热软化效应是导致这一现象的主要因素。磨料磨损行为是冲击效应和磨削热耦合作用的结果。当切削速度为50 m/s时,磨损量最小。介绍
作为第三代半导体,碳化硅引起了人们的广泛关注。其去除机理和处理技术是研究的重点。然而,作为典型的硬脆材料,其加工效率远低于第一代半导体材料硅。随着超精密磨削设备的发展和应用,一些研究[1–6]表明,超精密磨削工艺可以有效提高单晶碳化硅的加工具有有效性,同时可以获得表面粗糙度小于1 nm的高质量加工表面[5]。 磨削过程中加工区域的能量密度和应变率高于其它加工方法,特别是在高速磨削/超高速磨削加工领域。磨料的刮擦速度直接影响塑性变形区的应变速率和温度分布[7],而磨削区材料的应变速率和温度分布与位错密度和平均位错速度有关。与静态/准静态去除机制不同,需要对高切削速度下的材料去除机制进行新的解释。 在加工过程中,磨料和工件之间的相互作用是复杂的[8–9 ],无法通过下式准确描述简单的经典款。为了分析加工过程中的材料去除机理,将一系列方法应用于该过程的分析。划痕模拟和实验是检查材料加工过程中去除行为的典型有效方法[10–12]。高速加工过程还涉及到温度、应变速率和刀具磨损等多种因素的影响,因此实验分析非常困难.应变率效应对材料去除机制的影响机制必须结合加工过程中微观组织的分布和演变来分析。限于目前的探测手段,这是通过简单的实验方法来实现。分子动力学方法可以用来研究物质分离过程中的键断裂过程和缺陷演化机理。可以得到纳米尺度下的非线性应力应变关系和损伤的形成与扩展过程。该方法可以充分解释单晶SiC在应变率效应和热软化效应影响下的去除行为。 目前,已经通过切削模拟对单晶碳化硅的微观去除过程进行了大量研究,如塑性去除机理[13–22],加工参数(各向异性、加工深度、刀具角度和工件初始温度)的影响规律[17,22–26]和磨料磨损机理[13–14,20–21]。其中,一些学者进行了初步分析了切削速度对应变率效应的影响。Noreyan等人[16]研究了切削速度对材料机械响应特性(摩擦系数、划痕硬度和磨损)和塑料去除机制的影响。研究发现,摩擦系数和划痕硬度随着切削速度的增加而降低,加工区域的非晶相随着切削速度的增加而增加。Goel等人[23]认为,随着切割速度的降低,碳化硅的变形机制从非晶化(切割速度为10 m/s和100 m/s)变为“解理断裂”(切割速度为4 m/s)。 首先,位错运动和分布形式是影响单晶碳化硅塑性去除方式和亚表面质量的重要因素。从目前的研究成果来看,缺乏应变率对位错运动影响机理的研究,切削速度引起的应变率效应和热软化耦合效应的影响较少。其次,为了节省计算时间和简化分析过程,在碳化硅切削仿真中,一般将金刚石刀具简化为刚体。然而,金刚石砂轮在磨削碳化硅材料时磨损严重。如何减少砂轮磨损已经成为困扰业界的一个问题。因此,深入分析切削速度对加工过程中磨粒磨损行为的影响规律具有现实的指导意义。方法学
本文中的切削模拟是通过大型原子/分子大规模并行模拟器(LAMMPS)软件完成的。如图1(a)-(c)所示,磨粒模型和3C-碳化硅工件模型分为三部分:边界原子层、恒温原子层和牛顿原子区。模型的底层和左侧层是固定的,主要用于减少边界效应,保持晶体对称性。原子的这一部分叫做边界层。靠近边界层的原子作为恒温层放置,以保持它们的温度不受切割过程的影响。牛顿区原子遵循基本牛顿力学,位置和状态由势函数决定。为了避免硬边界反射对人体结构研究的影响,应减小模型的尺寸,并在模型两侧使用周期性边界条件。 模拟过程中使用的磨粒模型如图1(b)所示,球形为球冠三棱锥,边对边夹角为90°,磨粒的尖端半径为3 nm。在切削过程中,磨料被设定为可变形体,磨料在冲击过程中的变形行为对计算结果的影响不可忽略。本文主要研究高速/超高速超精密磨削条件下单晶碳化硅的去除机理。考虑到模拟计算时间和实际磨削速度,切削速度设置为10米/秒、50米/秒、100米/秒、150米/秒和200米/秒 原子势函数对分子动力学模拟的准确性和可靠性起着至关重要的作用。根据以前对材料力学性能和单晶碳化硅加工去除机理的试验和模拟,Erhart和Albe提出的ABOP势函数是唯一可用的不抑制解理和断裂的三体势函数。这种势函数可以同时反映二聚体和体性质,因此更适合模拟Si-Si、C-C和Si-C内部原子之间的相互作用。同时,作为多体势函数,ABOP势函数可以用来模拟形成 和化学键断裂,解释了切削过程中的材料去除行为和磨损。因此,本研究采用ABOP函数来模拟单晶碳化硅的切割[14,22–23,26–27]。 lang; rang; 切削模拟在(001)基面(垂直于z轴)上沿方向100(x轴的正方向)进行。利用OVITO软件,结合位移提取算法(DXA),分析了材料在切削过程中的变形和去除机理。结果和讨论
表面/次表面材料去除特征分析 从图2可以看出,实际加工深度仅在初始接触区域接近预设深度。由于金刚石磨粒磨损和材料弹性回复的影响,稳定加工阶段的剩余加工深度低于预定加工深度的50%。同时,切削速度对碳化硅材料的实际去除量具有显著影响。当切割速度等于50米/秒时,可获得最大实际加工深度。在较低(10米/秒)和较高(100米/秒、150米/秒和200米/秒)切割速度下,材料去除量明显小于50米/秒。 图2中白色原子区域的晶格严重扭曲。失去闪锌矿金刚石结构的碳化硅转变成存在于加工表面和芯片中的非晶态。这3C-碳化硅的加工表面被非晶层覆盖。3C-SiC纳米切削过程中存在从有序到无序的结构转变。此外,非晶层的厚度与切削速度密切相关。在50 m/s的切削速度下,材料去除量最大,并且表面残余非晶层的厚度也最大。切割速度超过50 m/s后,表面残留非晶层的厚度随着切割速度的增加而减小。切削速度对材料去除模式也有显著影响。当切削速度小于100 m/s时,切屑中有完整3C结构的纳米颗粒残留。这一现象表明,即使理论加工深度仅为5 nm,在3C-SiC去除过程中也存在脆性分离现象。因此,增加切割速度有利于SiC材料的完全塑性去除。 除了非晶相之外,在加工表面/亚表面上还发现了大量的位错。残余位错线的深度决定了损伤层的深度。如图3所示,损伤层深度远大于剩余加工深度,两者之比超过3∶1。目前,位错层三维分布的检测是非常困难的,在加工初始阶段减小位错线的深度是提高加工质量最有效的手段。当切削速度等于150 m/s时,亚表面损伤层的深度最大。较低或较高的切削速度有利于降低加工表面下的损伤深度。加工区域的应变速率对加工区域中残余位错的密度和深度有显著影响。因此,研究切削速度对位错运动和分布的影响机理具有重要意义。 位错分布及运动机理分析 3C-SiC具有典型的闪锌矿结构,是{111}面的双层堆垛结构。两个连续的双层之间具有宽间距的表面被称为集,而双原子表面之间具有窄间距的表面被称为滑移集。3C-SiC的主要滑移系有:滑移{111}/ lt; 112 gt;和集{111}/ lt; 110 gt;。glide { 111 }/lt; 112 gt;(0.3157 ev/a2)的广义层错能低于集的GSFE { 111 }/lt; 110 gt;(0.5 eV/omega;2),所以SiC材料中的位错滑移运动在相同条件下更倾向于滑移{111}/ lt; 112 gt;。然而,位错运动与切割面的晶体学取向和切割方向密切相关。在(001)面上沿[100]方向切割时,位错运动形式主要是普通滑移系{111}/ lt; 110 gt;的滑移运动,位错类型主要是柏式矢量为1/2 lt; 110 gt;的完全位错。 如图4所示,损伤区内存在大量柏式矢量为1/2 lt; 110 gt;的完全位错,少量柏式矢量为1/6 lt; 112 gt;的圆形和半圆形部分,柏式矢量为1/3 lt; 111 gt;的Frank型固着部分,柏式矢量为1/6 lt; 110 gt;的阶梯杆部分,以及其它类型的位错结构。对于ABOP势函数,碳化硅材料的孪晶错能与不稳定堆垛层错能的比率更高,孪晶形成的能垒高于位错成核的能垒[27]。因此,亚表面损伤形式主要是位错,没有发现孪晶结构。 通过比较磨粒的切削方向、加工的晶面和相应的滑移系,可以推断出 滑移系(111̄)∕[01̄1̄)和(11̄1̄)∕[011̄)的施密德因子为0.33, 而滑移系的施密德因子(11̄1̄)∕[110)和(111̄)∕[11̄0)是 0.46.然而,考虑到磨料刀片的钝化效应,除了垂直于磨料前接触表面的力之外,还有沿[001̄]方向的挤压力,相应的施密德因子分别为0.408和0.0。因此,仅考虑加工方向与滑移系之间的关系,整个切削过程中的滑移运动应优先在滑移系(111̄)∕[01̄1̄)和(11̄1̄)∕[011̄].)上进行从图4可以看出,当切削速度等于10 m/s时,位错滑移运动主要发生在两个滑移系(1̄11)∕[011̄)和(11̄1̄)∕[011̄)上,这与计算结果基本一致。当切削速度等于50 m/s和100 m/s时,亚表面区域的位错主要是具有伯格斯矢量1/2[01̄1̄].的完全位错当切削速度达到150 m/s和200 m/s时,具有柏式矢量1/2110的理想位错线的长度达到最大值减少,位错的形式失去规则性。根据位错的滑移系,滑移运动形式基本上处于随机分布状态。 磨料模型理论上是一个三棱锥结构,在z轴上有三重对称轴。当沿着切割时[100]方向,磨料两侧碳化硅材料的相应滑移面应具有相同的施密德因子。从图4中可以看出,当切割速度为10 m/s时,位移的分布是复杂的。这种分布规律与磨料运动过程中的磨损行为密切相关。剪应力的值为图5。当切削速度等于10米/秒时,在(a) 4.3纳米和(b)45.2纳米的切削距离处的磨料尖端形貌。(c)是(a)和(b)的方向。图6。不同切削速度下的位错长度分布,(a)-(d)是对应于柏式矢量other,1/2 lt; 110 gt;,1/2 lt; 112 gt;和1/6 lt; 111 gt;的位错线长度,(e)是位错线总长度,(f)是切削速度等于50 m/s时不同的柏式矢量下的位错分布在切割过程中,驱动磨料两侧的相应滑动系统是不同的。如图5所示,由于最初的冲击而发生磨损。磨料刀片的形状是不规则的。接触应力对具有伯格斯矢量1/2[011̄形核和在沟槽左侧区域扩展的位错更有利。然而,随着切削过程和磨料磨损的进行,接触区域中的应力更有助于凹槽左侧区域中的伯格斯矢量1/2[011̄位移的成核和扩展。当切削速度为50 m/s和100 m/s时,伯格斯矢量1/2[01̄1̄位错主要分布在沟槽右侧。除完全位错外,其它类型位错的变化图6显示了切割速度与切割长度的关系。具有1/6112 柏式矢量的Shoreley分支长度随切削速度的增加而增加。这是因为滑移系滑移{111}/ lt; 112 gt;中的滑移运动受温度影响很大[27]。增加切割速度导致切割区域的温度更高,这有利于触发形核和扩展滑移系中的位错滑移{111}/ lt; 112 gt;。的长度随着切削速度的增加,Burgers矢量为1/3 lt; 111 gt;的Frank型无柄部分逐渐减少。 应变率effect和温度effect的影响机理分析 为了研究切削速度对碳化硅去除过程中应力和温度分布的影响机理,本文采用以下公式得到不同切削速度下的应力和温度分布。为了分析温度效应对基体材料变形机制的影响,将忽略与基体分离的碎片部分。 温度计算的公式为: ?? ? 其中EK是系统的动能,N是原子数,vi代表第I个原子的速度,T是系统的温度,K是玻尔兹曼常数,等于1.3806503times;1023J/K,T是原子的温度。 静水压力的表达式为: ϭhyd是静水压力,?1,?2和?3是主应力。 SiC材料在挤压作用下的材料变形主要是由刮擦过程中非晶区的弹性变形、位错滑移运动和剪切运动来适应的。从图7可以看出,位错长度dld/dt的增长率随着切割速度的增加而增加。之间的拟合关系 二是: lt;剩余内容已隐藏,支付完成后下载完整资料
资料编号:[588840],资料为PDF文档或Word文档,PDF文档可免费转换为Word
您需要先支付 30元 才能查看全部内容!立即支付
课题毕业论文、文献综述、任务书、外文翻译、程序设计、图纸设计等资料可联系客服协助查找。